WJE PROJECTS
High-Pressure Vessel Design
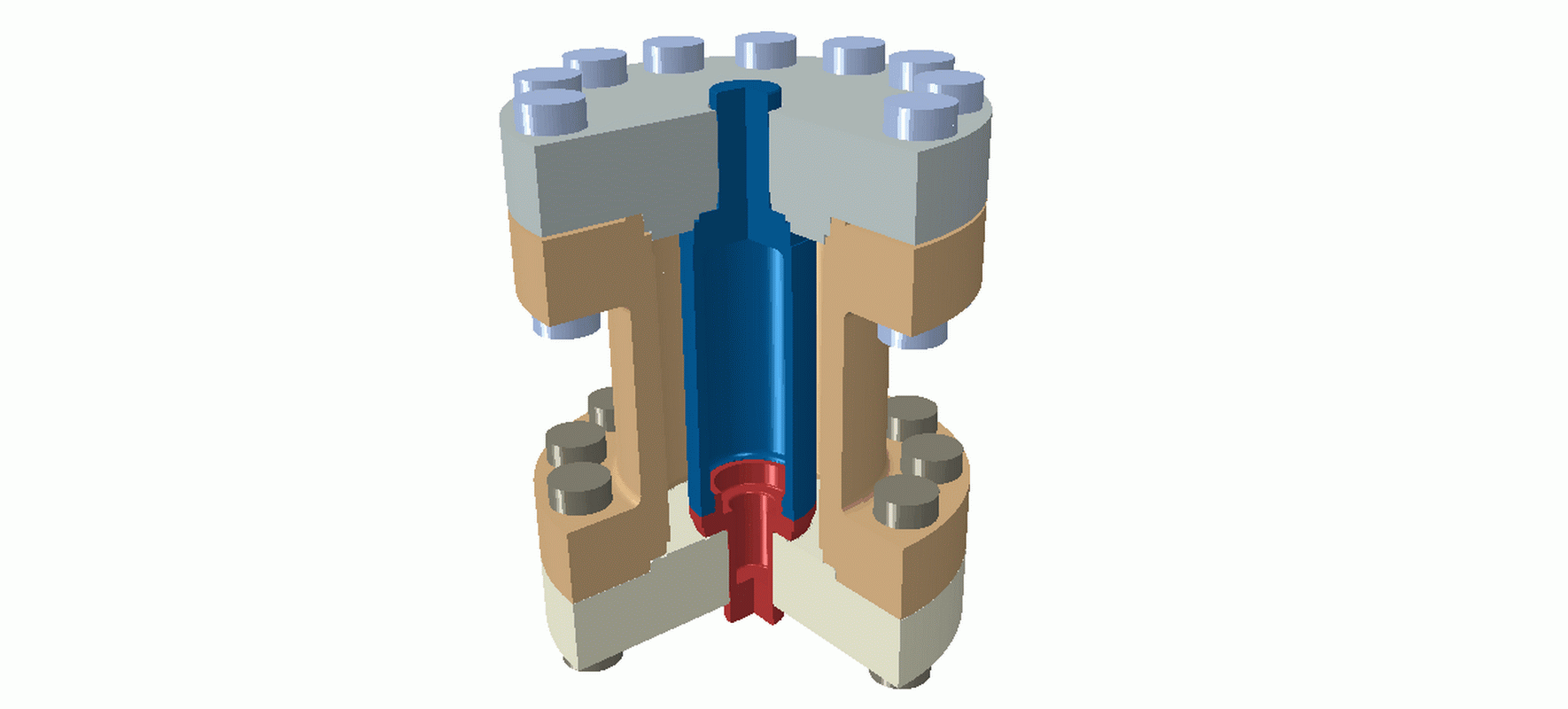
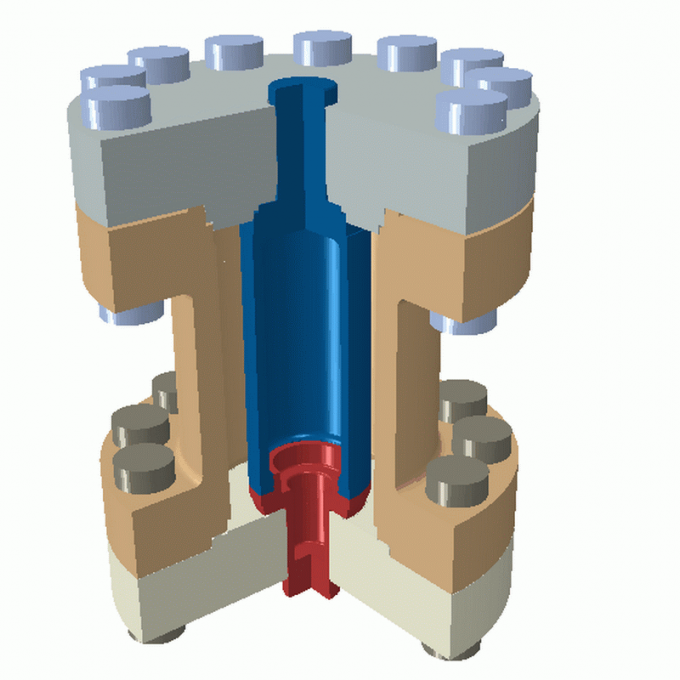
CLIENT |
Confidential |
LOCATION |
Houston, TX |
Design and Analysis of Small Vessel Used for Well Cement Testing
WJE was asked to evaluate a small pressure vessel used for testing according to the design principles in ASME Boiler and Pressure Vessel Code, Section VIII, Division 1 with a nonlisted material of construction. The design by analysis assessment considered relevant load combinations listed in the code to evaluate applicable failure modes, including plastic collapse, buckling, and cyclic service. The overall objective was to establish that the vessel design was safe to operate based on engineering judgement and best practices in vessel design by analysis.
BACKGROUND
Inherent design margins from the ASME Boiler and Pressure Vessel code rely on comprehensive rules governing all aspects of vessel design, materials, fabrication, pressure testing, and nondestructive examination. In scenarios where a designer or fabricator deviates from those requirements, the ultimate design margin of the vessel may be higher or lower than that of a code stamped vessel. In this case, the client elected to perform supplemental design by analysis to ensure protection against the relevant failure modes when using materials not classically permitted for pressure vessel use.
SOLUTION
The laboratory-scale pressure vessel is used to perform high-pressure, high-temperature testing on well cement slurries. The cylindrical pressure vessel design has flanged and bolted end closures with multiple high-temperature metal seals. The unique design includes two concentric pressure chambers to allow for cement in the annular space to be functionally tested under applicable confinement and directional loading.
WJE used detailed finite element analysis of transient, thermo-mechanical loading to predict thermal gradients and stresses during the prescribed test protocol and capture complex interactions between mating components. Based on the primary failure modes, established best practices in vessel design by analysis were used to demonstrate that the test vessel was safe to operate at the required temperature and pressure and had sufficient fatigue capacity to support the intended test protocol over the service life.
Through iterative analysis, several design modifications were identified by WJE to improve functionality and overall performance of the vessel. WJE was able to assure the client that the test vessel can be safely operated in the laboratory environment with personnel working in close proximity by recommending a best practices approach to supplemental material toughness testing, nondestructive examination, fabrication, and pressure testing of the vessel.
RELATED INFORMATION
-
Our metallurgical and applied mechanics engineers provide solutions related to design... MORE >Services | Metallurgy and Applied Mechanics
-
WJE metallurgical and welding consulting engineers have extensive experience in the... MORE >Services | Metallurgical Consulting
-
We provide dedicated engineering support and specialized testing services for all sectors across... MORE >Markets | Energy
-
WJE fracture mechanics consultants have provided fracture mechanics assessment and fitness for... MORE >Services | Fracture Mechanics Assessment and Fitness for Service