WJE PROJECTS
Cyclic Service Vessel
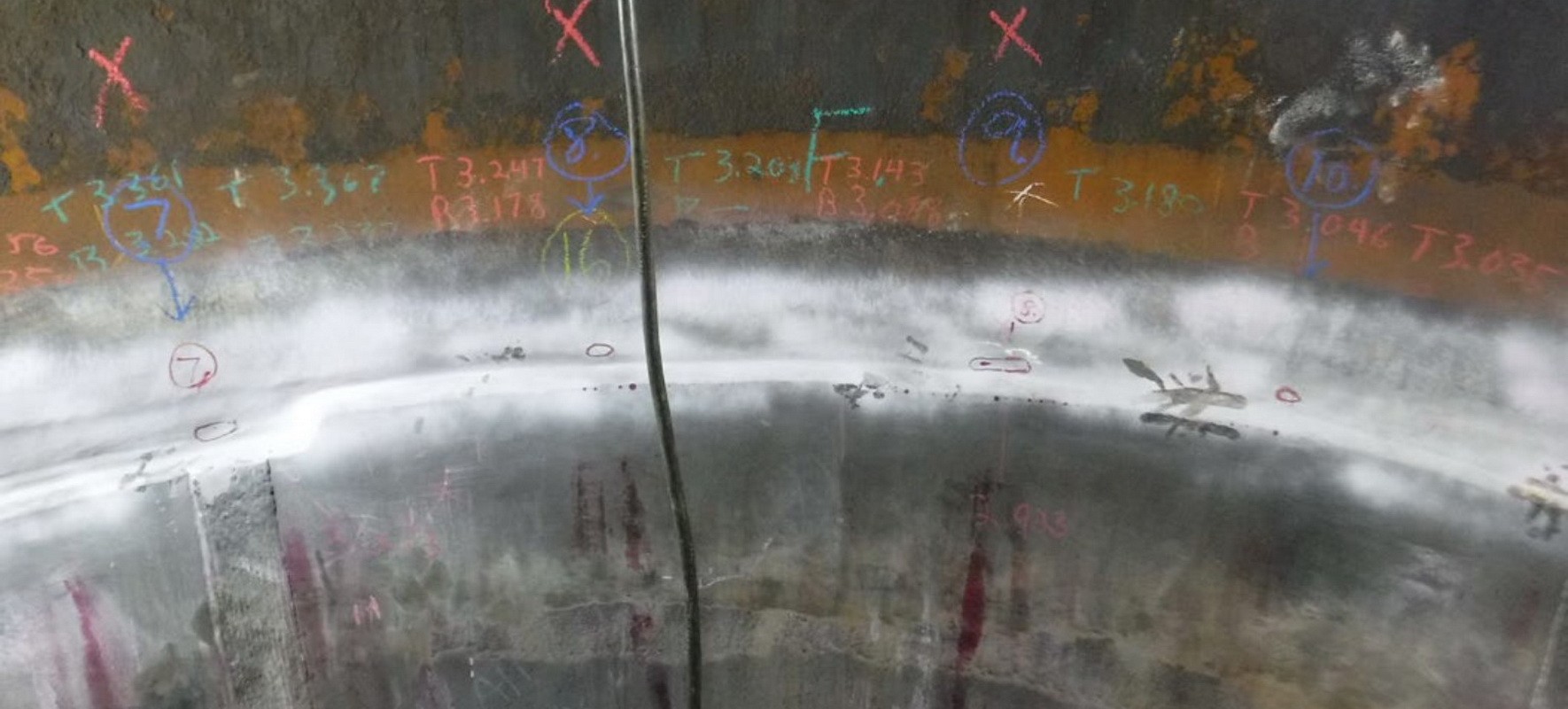
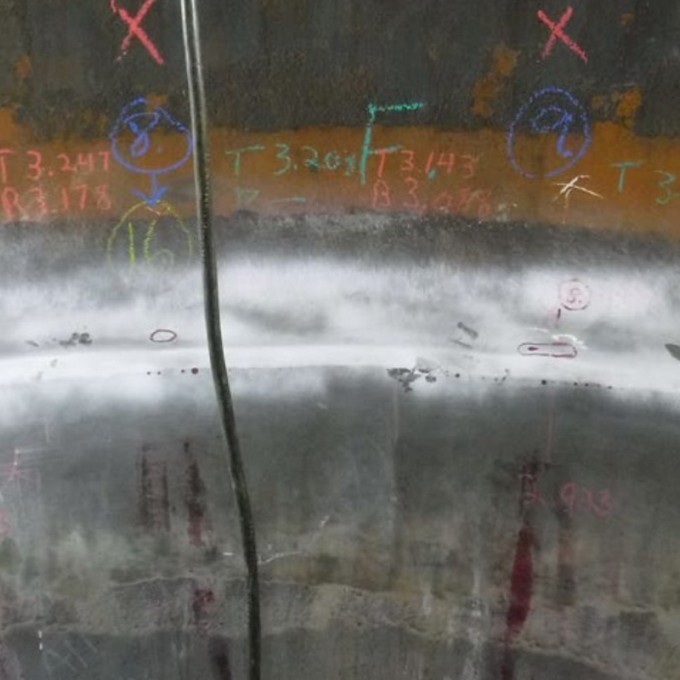
CLIENT |
Confidential |
LOCATION |
Midwest |
API 579 Fitness for Service Assessment of Crack-Like Indication
WJE was asked to perform a Fitness for Service (FFS) assessment to evaluate crack-like indications found at the circumferential seam between a toricone head and cylindrical shell. During an external inspection of the fatigue sensitive location, ultrasonic (UT) testing identified a surface breaking flaw at the inner surface. The objective of the effort was to evaluate the in-service damage including the potential for crack growth and estimate the remaining life to allow the facility to plan for an outage and execute any necessary repairs.
BACKGROUND
The high-pressure feed vessel was designed and fabricated according to ASME Boiler and Pressure Vessel Code Division 2 rules. This standard includes more stringent limits on material ductility and toughness, enhanced examination of the pressure boundary, and requires that the designer address cyclic loading and fatigue performance. The 10’-6” ID by 10’ overall length vessel was fabricated from 3.5-inch-thick steel plate with an explosion bonded corrosion resistant alloy cladding. The design consists of rolled and butt-welded shell courses, with a toriconical bottom head and outlet nozzle.
SOLUTION
WJE performed an FFS evaluation based on API 579-1 / ASME FFS-1 to determine whether the high-pressure feed vessel was safe to continue operating using Part 9, Assessment of Crack-like Flaws. The assessment used a Level 2 methodology to predict crack growth up to a limiting flaw or crack size under applicable operational cyclic loading provided in the User’s Design Specification (UDS).
Using the inspection data, a surface-breaking flaw was modeled using linear elastic fracture mechanics (LEFM) principals to evaluate the tendency of material failure due to both fracture and plastic collapse on a Failure Assessment Diagram (FAD). The evaluation included the influence of stress concentration effects, differential thermal expansion, and residual stresses at the welded joint by extracting driving stresses from a finite element model of the vessel. Material toughness values were estimated using the material test reports (MTR) data and weld qualification records furnished during vessel fabrication. Several sensitivity studies were performed to understand the influence of environmental exposure, modified operational parameters, and median toughness.
The assessment predicted relatively fast crack growth in all scenarios with a remaining life between four and fourteen weeks. The FFS assessment provided the necessary data to prioritize and plan a facility outage to perform repairs. In addition, WJE recommended an inspection interval and NDE technique to monitor the indication in-service prior to repair.
RELATED INFORMATION
-
Our metallurgical and applied mechanics engineers provide solutions related to design... MORE >Services | Metallurgy and Applied Mechanics
-
We provide dedicated engineering support and specialized testing services for all sectors across... MORE >Markets | Energy
-
WJE metallurgical and welding consulting engineers have extensive experience in the... MORE >Services | Metallurgical Consulting
-
WJE fracture mechanics consultants have provided fracture mechanics assessment and fitness for... MORE >Services | Fracture Mechanics Assessment and Fitness for Service